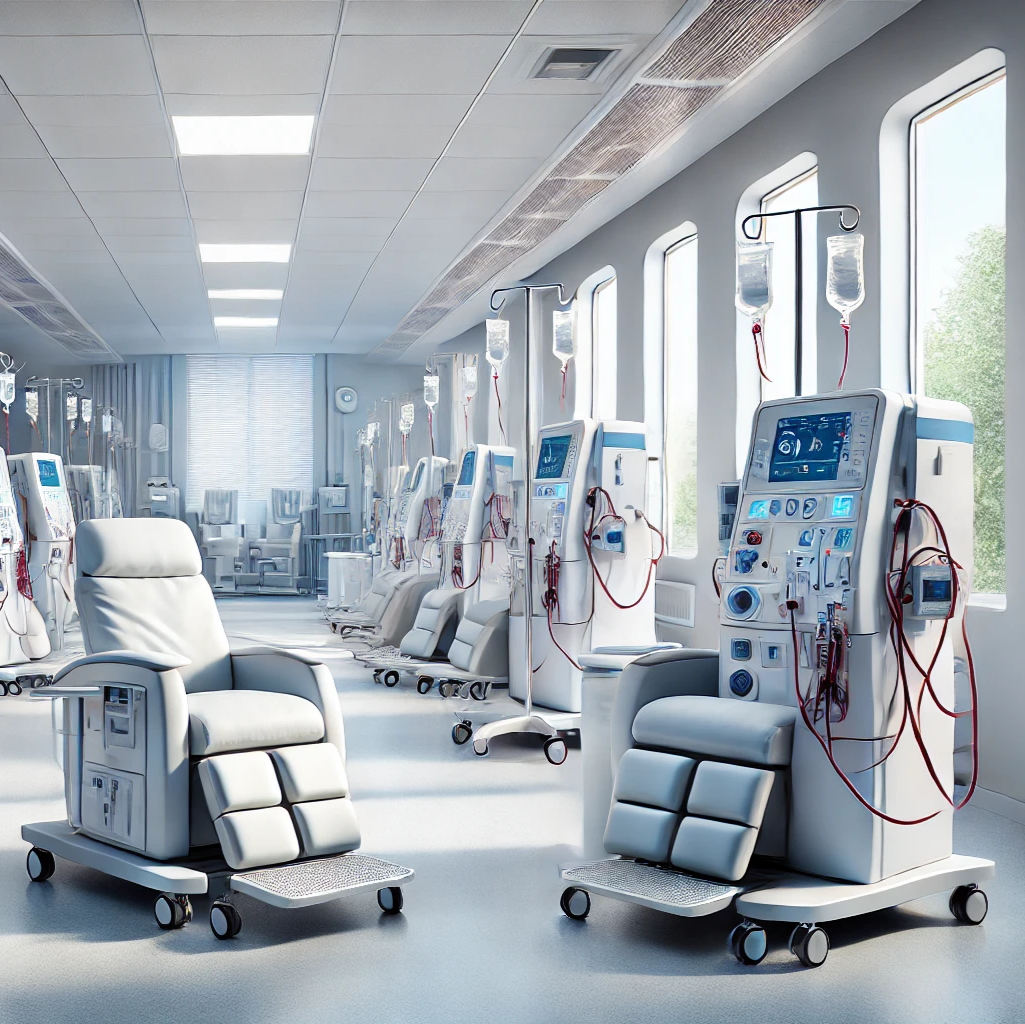
The financial considerations of buying and operating a hemodialysis (HD) machine are crucial for dialysis centers, hospitals, and healthcare providers who manage patients with kidney failure. These costs encompass not only the initial purchase but also the long-term operational expenses required to maintain and effectively use the equipment. Below is an analysis of the major cost components involved in purchasing and operating a hemodialysis machine.
1. Initial Purchase Cost
The cost of a new hemodialysis machine typically ranges from \$10,000 to \$15,000 per unit, although prices can vary based on the brand, features, and capabilities of the machine. High-end models or those with advanced monitoring and safety features may exceed \$20,000. Used or refurbished machines are also available and can cost approximately 40-50% less, depending on their condition and warranty status.
Some factors affecting purchase costs include:
- Brand and Model: Machines from leading manufacturers, such as Fresenius, Baxter, or B. Braun, often command higher prices due to reliability and advanced features.
- Customization: Certain machines can be tailored with optional features, such as biofeedback mechanisms, which adjust dialysis parameters in real-time for individual patient needs.
- Integration: Machines with interfaces for electronic medical records (EMR) systems or patient monitoring software may have additional upfront costs.
2. Installation and Facility Preparation
Beyond the machine cost, installation and facility modifications can contribute significantly to the overall expense:
- Electrical and Plumbing Setup: Dialysis machines require specialized electrical outlets, reliable water supply, and drainage systems to support the high volumes of purified water used in dialysis. Installing these systems can cost between \$5,000 and \$15,000.
- Water Treatment System: To meet the strict standards for dialysis water purity, healthcare facilities typically install a reverse osmosis (RO) water treatment system, which can range from \$10,000 to \$40,000 depending on capacity and system complexity.
- Compliance and Safety: Meeting regulatory standards, such as those from the FDA and Centers for Medicare & Medicaid Services (CMS), may involve additional expenses for safety equipment, signage, and facility upgrades.
3. Consumables and Operational Supplies
Operating an HD machine requires continuous use of consumables, such as:
- Dialyzers and Tubing: Dialyzers (filters) and tubing are typically single-use items, though some centers reprocess them. Each session costs approximately \$10-\$20 for tubing and \$15-\$50 per dialyzer.
- Dialysate Solution: Dialysate costs range from \$5 to \$10 per session, depending on patient requirements and the number of sessions per week.
- Water and Electricity: HD machines consume significant water and electricity, especially considering that many patients undergo three to four treatments weekly. Monthly water costs can vary widely, while electricity costs generally add about \$200-\$300 per month per machine.
4. Maintenance and Technical Support
Routine maintenance is essential to ensure the functionality and safety of HD machines. Maintenance expenses may include:
- Service Contracts: Many providers choose a service contract with the manufacturer or a third-party company for preventative maintenance and troubleshooting. These contracts can cost between \$1,000 and \$5,000 annually per machine, depending on coverage levels.
- Repairs and Replacement Parts: Machines are subject to wear and tear, especially in high-use centers. Minor repairs (e.g., replacing a motor or pump) can cost a few hundred dollars, whereas major repairs (e.g., circuit board replacement) may run into thousands. Replacement parts and labor costs can average \$2,000 annually.
- Calibration and Quality Assurance: Regular calibration ensures machine accuracy, and many centers adhere to strict quality assurance protocols to maintain compliance. This can add another \$500-\$1,500 per year per machine.
5. Staffing and Training
Operating hemodialysis machines requires specialized training for staff, particularly dialysis nurses and technicians:
- Staff Wages: Dialysis technicians and registered nurses oversee HD sessions. Annual wages for dialysis staff vary by region but generally range from \$50,000 to \$90,000 for technicians and \$60,000 to \$100,000 for nurses.
- Training and Certification: Initial training and ongoing education for staff are essential. Training costs include both certification expenses (typically \$200-\$500 per staff member) and potential downtime costs while staff members attend certification courses.
6. Regulatory and Compliance Costs
In the United States, HD facilities must comply with federal and state regulations, which add to operational expenses:
- Inspection and Licensing Fees: Facilities undergo periodic inspections by CMS and may pay for licenses or certifications required to provide dialysis services. These fees vary but can add several thousand dollars annually.
- Reporting and Documentation: Compliance with reporting requirements (e.g., infection rates, patient outcomes) demands administrative effort, often translating to indirect costs associated with staff time and documentation software.
Total Cost Estimate
The combined cost of purchasing and operating an HD machine varies significantly based on utilization, maintenance requirements, and local cost factors. On average, the annual cost per machine in a high-use setting can range from \$20,000 to \$40,000 when accounting for consumables, maintenance, and operational supplies, excluding initial purchase costs.
Quiz
Please note that our articles are not intended to guide personal health decisions.
This content has been curated by Renes Care. Unauthorized use or reproduction is prohibited.
© Renes Care. All rights reserved.